The Role of Machine Settings in Reducing Chatter Machining
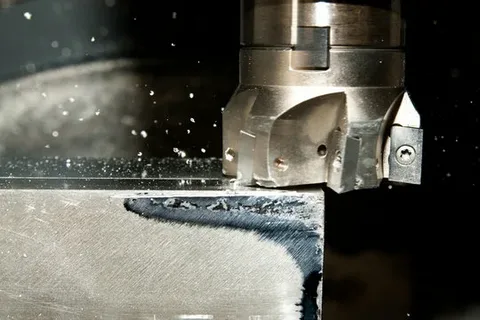
Chatter machining remains one of the most common and troublesome issues in manufacturing processes involving cutting tools, such as turning, milling, and drilling. It manifests as unwanted vibrations during the machining process, leading to poor surface finishes, reduced tool life, and decreased productivity. One effective way to minimize chatter machining is through proper machine settings. Adjusting parameters such as spindle speed, feed rate, and cutting depth can have a significant impact on controlling these vibrations. This article will explore how machine settings play a crucial role in mitigating chatter machining by optimizing the cutting process.
By understanding and manipulating these settings, manufacturers can achieve smoother operations, maintain consistent quality, and extend the life of both machinery and cutting tools. Proper machine settings not only enhance productivity but also ensure that machining operations are efficient and reliable. With that in mind, this article will examine the critical machine settings and how they interact to reduce the occurrence of chatter machining, thereby optimizing machining performance.
Understanding Chatter Machining and Its Causes
Chatter machining occurs when vibrations are introduced into the cutting system during the material removal process. These vibrations can lead to severe consequences, such as poor workpiece surface quality, uneven tool wear, and reduced production rates. At its core, chatter machining is typically the result of a dynamic interaction between the cutting tool, the workpiece, and the machine itself. These vibrations are usually amplified when the system encounters resonance frequencies, causing unstable cutting conditions.
Several factors contribute to chatter machining, including inappropriate feed rates, excessive cutting depth, worn cutting tools, or incorrect spindle speeds. Resonance in the system is a primary driver of chatter, as the frequency of vibrations aligns with the natural frequencies of the machine-tool system. Machine operators and engineers can combat these challenges by focusing on the role of machine settings to stabilize these variables, adjust the cutting parameters, and minimize vibrational effects.
Spindle Speed and Its Influence on Chatter Machining
One of the most vital machine settings that can impact chatter machining is spindle speed. Spindle speed determines how fast the cutting tool rotates, and it plays a key role in influencing the stability of the machining operation. A poorly set spindle speed can lead to excessive vibrations, which in turn amplify chatter machining. Therefore, selecting an optimal spindle speed is essential for maintaining cutting stability and achieving high-quality machining.
The correct spindle speed reduces the likelihood of resonance and minimizes the chances of the tool cutting at a frequency that coincides with the natural frequency of the machine-tool system. Operators can optimize spindle speed by analyzing the workpiece material, cutting conditions, and tooling capabilities. Modern CNC machines often come with programmable spindle speed controls, allowing precise adjustments to avoid crossing resonance thresholds, thereby ensuring steady cutting operations.
Feed Rate Adjustments to Minimize Chatter
The feed rate refers to how quickly the cutting tool moves across the workpiece during the cutting operation. It is another crucial machine setting that influences the incidence of chatter machining. A feed rate that is too high can push the cutting system into unstable dynamic conditions, thereby encouraging chatter. Conversely, a feed rate that is too low can lead to inefficient material removal and longer production times.
To minimize chatter machining, operators must find the optimal feed rate that balances cutting performance and stability. By conducting trial runs and analyzing machining performance, engineers can determine the ideal feed rate that avoids resonance and allows for smooth tool interaction with the material. Advanced CNC machinery can automatically adjust feed rates in response to real-time feedback, making it easier to maintain stable operations and avoid chatter vibrations during the cutting process.
Adjusting Cutting Depth for Stable Machining
Cutting depth, or the amount of material removed by the cutting tool during each pass, is another critical parameter that influences the occurrence of chatter machining. When the cutting depth is too great, the machine's cutting system may experience excessive force, leading to unstable conditions and increasing the likelihood of chatter. On the other hand, a shallow cutting depth may not be sufficient to achieve the desired material removal rate, reducing efficiency.
Machine operators can reduce chatter machining by carefully controlling the cutting depth to ensure that the cutting tool operates under stable and predictable conditions. By selecting appropriate cutting depths, manufacturers can prevent excessive cutting forces that may trigger vibrational responses. In many cases, using variable cutting depths or employing multiple passes with shallower depths can help reduce the effects of chatter while maintaining productivity and achieving high-quality finishes.
Optimizing Machine Stiffness and Damping to Combat Chatter
Aside from spindle speed, feed rate, and cutting depth, machine stiffness and damping are additional factors that affect chatter machining. Machine stiffness refers to the structural rigidity of the machine tool system and its ability to resist deformation during operation. A machine with insufficient stiffness can amplify vibrations, leading to chatter. To combat this, operators should ensure that the machine's structural components are properly maintained and robust enough to withstand the dynamic forces involved in machining.
Damping plays an important role in absorbing and dissipating vibrational energy within the machine-tool system. Incorporating effective damping mechanisms, such as vibration dampers and isolators, can significantly reduce the impact of vibrations and minimize chatter machining. Properly tuned machine settings combined with enhanced damping capabilities can create a more stable and controlled cutting environment, which improves the overall machining performance and extends tool life.
Conclusion
Chatter machining is a persistent issue in manufacturing that leads to decreased tool life, poor surface quality, and reduced production efficiency. However, by carefully adjusting and optimizing machine settings, such as spindle speed, feed rate, and cutting depth, manufacturers can effectively mitigate the effects of chatter and maintain stable cutting operations. Additionally, improving machine stiffness and utilizing effective damping can enhance stability and reduce the chances of resonance-induced vibrations.
Understanding the role of machine settings in reducing chatter machining allows manufacturers and machine operators to take a proactive approach to minimize unwanted vibrations. This optimization not only leads to better surface finishes and improved tool life but also enhances the overall productivity of the machining process. With advanced technology and a keen understanding of cutting dynamics, reducing chatter machining has become an achievable goal, ensuring a smoother, more efficient, and more profitable manufacturing operation.
- Art
- Causes
- Crafts
- Dance
- Drinks
- Film
- Fitness
- Food
- Oyunlar
- Gardening
- Health
- Home
- Literature
- Music
- Networking
- Other
- Party
- Religion
- Shopping
- Sports
- Theater
- Wellness