Water Jet Cutting Advantages and Disadvantages - What is Swiss Machining & Swiss Precision Machining
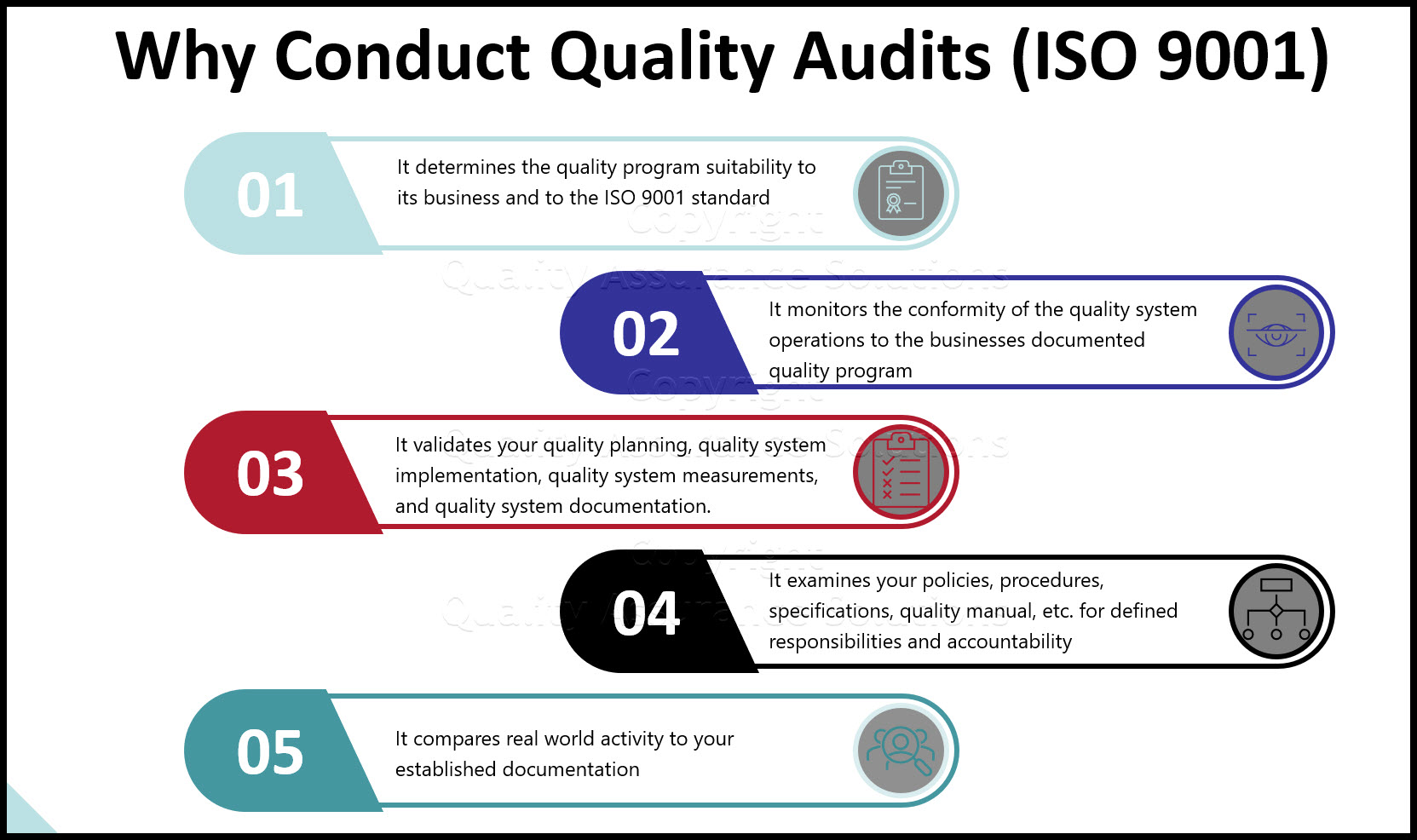
Tolerances are very tight. The Swiss machine securely holds the workpiece next to the processing region, ensuring that the component retains its stability and is virtually completely unaffected by tooling force during processing. Thus, even when cutting very tiny components, it is possible to guarantee that the PM services remains within a very narrow range of acceptable error.
Reduced price. Due to the fact that Swiss type lathes can handle bar stocks of smaller sizes, machined component makers may stock smaller materials at a cheaper cost. The automation of Swiss CNC machining, on the other hand, lowers the cost of labor while simultaneously shortening the lead time.
High degree of adaptability. Although IPC services are capable of processing tiny components, they also have the ability to manufacture parts that are longer, thinner, and more complicated in their design. Swiss machines are also capable of producing complex components with thinner walls, finer features, and deeper cuts that would be difficult or impossible to create with other types of machinery.
In the production operations of many industries, sheet metal cutting is a critical activity that must be completed accurately and efficiently. When working with materials such as steel, this procedure is performed after each material has been acquired via a preparatory step. Aside from that, in order for the end product to be changed, it must first go through a transformation, in which this cut is very essential. With the advancement of technology, we now have a greater variety of metal cutting techniques to choose from, but the shearing cut remains the most conventional and frequently utilized. Sheet metal shear cutting is a mechanical method for straight cutting sheet metal that is characterized by the use of two blades that move against each other throughout the cutting process. It is based on a crushing process that is followed by a partial penetration cut into the surface of the component. The cutting portion is fractured throughout the remainder of the cutting section, with no chip removal.
Plasma Cutting Advantages and Disadvantages - What Is Plasma Cutting and How Does It Work? What Is Plasma Cutting and How Does It Work?
Water jet cutting is a mechanical technique that allows for the cutting of a material by causing a jet of water to hit on it at a rapid rate, resulting in the desired finish being achieved. Cut processing by water jet (WJ) is accomplished by pressurizing water to a maximum pressure of 600MPa (about 6,000 atm), injecting it via a tiny diameter nozzle (0.1mm), and using the energy of high-speed, high-density ultra-high pressure water. It is a technique for cutting through an item. A damaging water jet is created when the water is compressed by the ultra-high pressure water production pump, which travels at about three times the speed of sound (WJ). Swiss precision machining and Swiss turning are both cost-effective methods for producing a large number of tiny, complicated components in large quantities.
In this sheet metal cutting procedure, the parts that have a certain form and specified dimensions are separated from the ones that do not. It is typically done in the vicinity of drilling and milling machines, as well as in other operations carried out by machines and involving the employment of a variety of cutting instruments. Detaching the metal in the form of tiny chips allows for the production of the components, which may be accomplished via a variety of methods such as laser cutting and others that can vary based on the need. Perfect cuts are only possible with a high-quality shear that minimizes the impact of changing sheet metal composition, internal tensions built up over time, and geometrical constraints. If these natural impacts are not rectified and compensated for, they may manifest themselves as flaws in completed goods, lowering the overall quality of the finished product.
Nd:YAG laser cutting using neodymium doped yttrium-aluminum garnet - What is a Swiss CNC Machine, and how does it work?
In the industrial industry, Swiss machining is a process in which a specific tool and feeding technique are used to machine stock into complicated or elaborate components with strict tolerances. Swiss precision machining is the process of cutting workpieces using Swiss-type CNC lathes that spin components in a radial motion as the workpiece is being turned. In Switzerland, the Swiss machining technique and the Swiss-type machine were developed in the 19th century in response to the demand from Swiss watchmakers, which made them distinct from other conventional lathes when fabricating small complex parts. The inventor of the Swiss machine is Jakob Schweizer, who devised a new method of sliding parts along the longitudinal axis of the lathe rather than moving parts down.
This page covers the many sheet metal cutting techniques that may be performed without the use of shearing. The working principle of each, as well as the benefits and drawbacks of each, as well as their various areas of use, are discussed in detail. Among the most important processes in the sheet metal fabrication industry, metal cutting is one of the most common. Shearing is one of the most common sheet metal cutting processes, and it is performed by means of machines called shears, which consist of blades that act on the metal in order to make the cut. When it comes to conductive materials (such as brass, copper, aluminum, or steel), plasma cutting is a great instrument to employ, which is why it is often used in factories, weld shops, car repair, restoration, industrial building, and operations. demolition.
- Art
- Causes
- Crafts
- Dance
- Drinks
- Film
- Fitness
- Food
- Games
- Gardening
- Health
- Home
- Literature
- Music
- Networking
- Other
- Party
- Religion
- Shopping
- Sports
- Theater
- Wellness