The biggest challenges facing the chemical suppliers supply chain in 2020
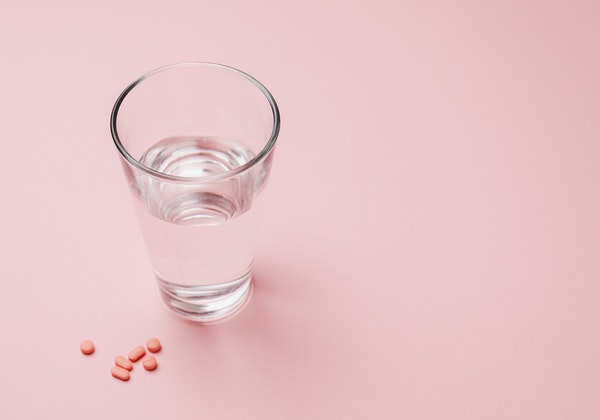
Covid-19 continues to disrupt the world economy, even in countries where the pandemic is under control. In addition, despite the pressure on economic recovery and operation, persistent uncertainty, lack of consumer confidence and supply chain challenges continue to constitute constraints.
The latest forecast of the International Monetary Fund shows that the GDP of the United States in 2020 is expected to be 8% lower than that in 2019, and the recovery in 2021 will be relatively slow.
When rumors about this dangerous virus first surfaced in December 2019, no one expected the extent to which it would spread, nor the human and economic damage it would cause. Supply chains, especially those that rely on international trade, have been hit the hardest. The weakness of the systematic supply chain is exposed. Although all enterprises are affected, the enterprises that fail to keep up with the trend of the key supply chain are the hardest hit. Looking ahead, as companies scramble to rebuild supply chains and restart production, they need to consider six key challenges in the supply chain of chemical suppliers.
The biggest challenge of chemical suppliers supply chain in 2020
Although it is unpopular, we need to accept the existence of a new normal before we find an effective vaccine or the virus mutates into a less harmful strain. This means that it is necessary to take safe actions, such as keeping social distance, wearing proper masks, and responding firmly to the almost inevitable surge of infections (threatening the supply chain, leading to local blockades and business disruption).
1. Limited data granularity
When China closed down, many people who thought they knew their own supply chain found that it was not enough to know only the first tier suppliers. Few people realize how much the closure of secondary and tertiary suppliers in Wuhan will affect supply as the virus spreads to other parts of the world. To a large extent, this is due to the wrong assumption of first-class suppliers, and it may also be wishful thinking to some extent. Novel coronavirus pneumonia, as governor of New York, said in his daily bulletin of new crown pneumonia, "let's start with facts. Although we all have our own opinions, let's start by reviewing the facts. "
2. Single source enlarges the risk of supply chain
For a variety of reasons, many companies focus on a single purchasing strategy, probably because it is considered the lowest cost scenario. Unfortunately, it also means that chemical suppliers are vulnerable if they face shortages or production disruptions. As Warren Buffett said, "only when the tide goes out can you find out who has been swimming naked all the time."
3. Slowing down digital conversion
Data acquisition is very important for effective decision-making. Unfortunately, many organizations have a hodgepodge of manual and digital systems that effectively trap information in functional silos, which means that decisions are hampered by incomplete images.
4. Keep the traditional inventory strategy
Traditional inventory control strategy focuses on the past performance to determine the current inventory strategy. Precise algorithms are used to determine precise requirements. The problem with this approach is that it doesn't take into account unexpected events, it's not agile, and it's often completely divorced from current reality.
5. Lack of operational data and insights
A common theme for business leaders, especially supply chain management, is that they often don't have enough information on hand to make informed decisions. In addition, the complexity of the supply chain makes it difficult for people to evaluate a variety of options, trade-offs and solutions, so as to get the best or correct decision.
- Art
- Causes
- Crafts
- Dance
- Drinks
- Film
- Fitness
- Food
- Games
- Gardening
- Health
- Home
- Literature
- Music
- Networking
- Other
- Party
- Religion
- Shopping
- Sports
- Theater
- Wellness